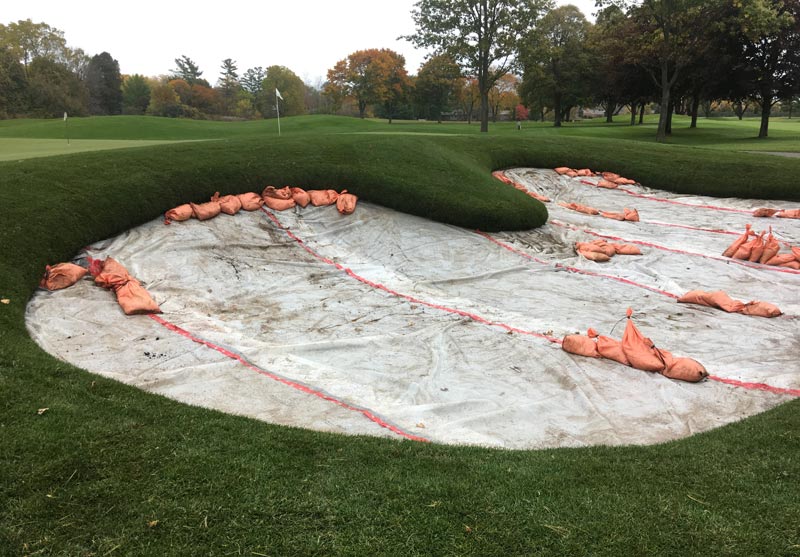
Edge of glory: The inverted-sod edge on one of the practice bunkers at London (Ontario) Hunt and Country Club. Superintendent Jayson Griffiths has been experimenting with the novel construction technique, with the goal of turning out cleaner, smoother, longer-lasting bunker edges. Photos courtesy of Jayson Griffiths
Perhaps time will tell whether Jayson Griffiths is a mad genius or simply mad. But this much is certain: Griffiths knows how to make a crisp, distinct, even unique bunker.
“I appreciate builders and architects,” says Griffiths, superintendent at London Hunt and Country Club in London, Ontario, and an 18-year GCSAA member. “And I have a passion for bunkers. There’s an art form to them.”
His masterpiece is on display in the form of one of the two bunkers at London Hunt and Country Club’s practice facility, of which the piece de resistance — pardon the French — is the edge Griffiths fashioned with an intricate inverted-sod technique.
Griffiths traces his bunker fondness to his days as an assistant superintendent at Devil’s Paintbrush Golf Club in Caledon East, Ontario, where he gained experience building and maintaining revetted bunkers made in the grand British tradition of stacking sod bricks vertically to create a fortifying — and potentially intimidating — bunker edge. Griffiths studied other bunker styles too, before and after moving on to his current position at London Hunt and Country Club in 2012.
Griffiths realized that bunkers, regardless of style, have limited life spans, and edges can be the “Achilles’ heel” over time, he says. “Environmental factors, sand splash, egress from improper golfer foot traffic, etc., all lead to eventual demise,” he says. “Bunkers fail over time. You’re constantly building and rebuilding.”
London Hunt and Country Club — originally designed by Robert Trent Jones in the 1950s and redesigned by Rees Jones in 2002 — has been working on a master plan with course architects Michael Hurdzan, Ph.D., and Chris Hurdzan of Hurdzan Golf Design, the centerpiece of which is the replacement of a dated, 38-year-old hydraulic irrigation system.
“Our infrastructure,” Griffith says, “is getting a little tired, like a lot of properties’.”
Bunkers came up as part of that master planning. They last were redone in 2006, and Griffiths was curious about the possibility of installing a matrix-style drainage and liner system in each of the course’s 63 bunkers, which total 120,000 square feet. Given the added cost of imported premium sand from Ohio, Griffiths wanted to do his due diligence to ensure membership would be pleased with the end result without any needless expenses.
He realized he had a perfect testing ground at the club’s 4-acre practice facility. He proposed renovating one of the facility’s practice bunkers with a Capillary Concrete system and the other with a Better Billy Bunker framework. He also suggested importing two kinds of sand and letting the members get a feel for their preference. Griffiths started looking for a contractor for the work, but found there wasn’t much interest in a small, one-off project, nor was there much availability before November 2019.
“So, it was either wait until spring or do it ourselves,” Griffiths says.
They opted for the latter. Over roughly two weeks last October, Griffiths and “a few” members of his staff renovated test bunker No. 1 around their other regular golf course tasks. Griffiths drew on his Devil’s Paintbrush days for the revetted-bunker-style exoskeleton, but the inverted-sod technique was an epiphany.
Determined to give the bunker shelf a solid foundation, Griffiths took a trip to the hardware store and returned with 102 concrete blocks, each 2 inches high and 14 inches long. Those blocks formed the foundation, atop which he stacked eight layers of sod with good, thick, established topsoil with the turf cut off. A traditional revetted bunker face is built at a 60-degree angle (too steep and it can collapse) stair-stepping away from the bunker’s center. Griffiths went rogue, stacking two rows vertically, then — “like the Leaning Tower of Pisa,” he says — angling inward toward the center of the bunker before retreating and creating a crude curve.
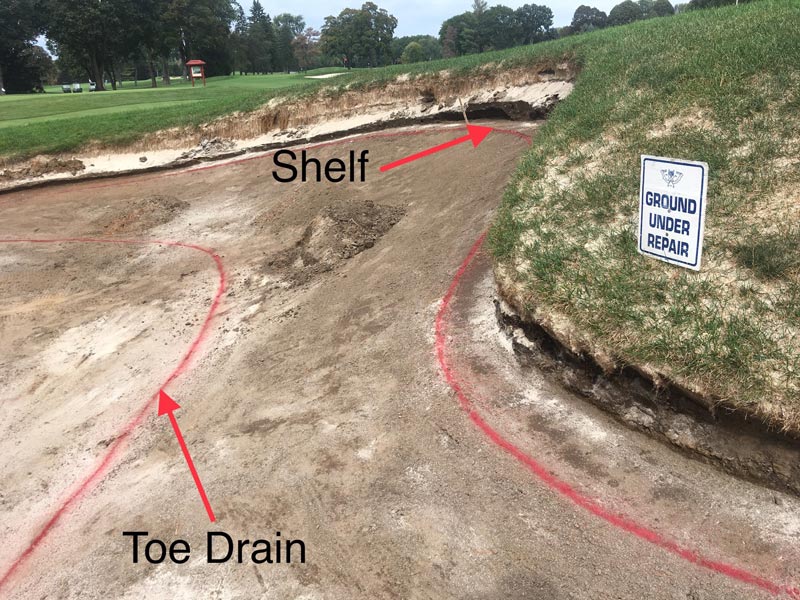
The practice bunker at London Hunt and Country Club prior to the renovation project that employed modified revetted edge construction.

Right: The “shelf” established for the concrete block perimeter.
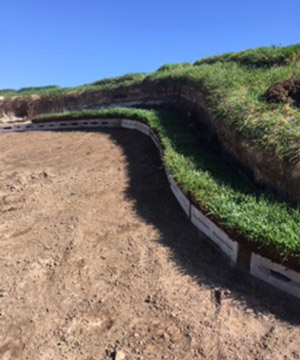
Right: Thick-cut, topsoil-rich sod stacked six to eight layers high. The final height is approximately 12 inches above the bunker floor.
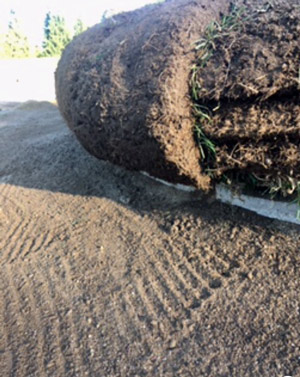
The inverted layer of thick-cut sod wrapped along the bunker’s edge ensures soil-to-soil contact and good rooting of the final turf.
Each row was tamped with a tamper, stapled and backfilled with soil. Griffiths wanted to sod over the face, but was concerned with how it would knit to the uneven surface. His solution: First turn the sod inside out.
“I took another piece of thick-cut sod, inverted it and wrapped it around, then stapled it like the edge of a couch,” Griffiths says. “It was really clean and smooth.”
The team finished work inside the bunker, sodded the edge traditionally — turfgrass side up, stapled to the inverted sod — and let it sit over the winter. The end result on full display this season is a distinct, smooth edge Griffiths describes as a “3D look.”
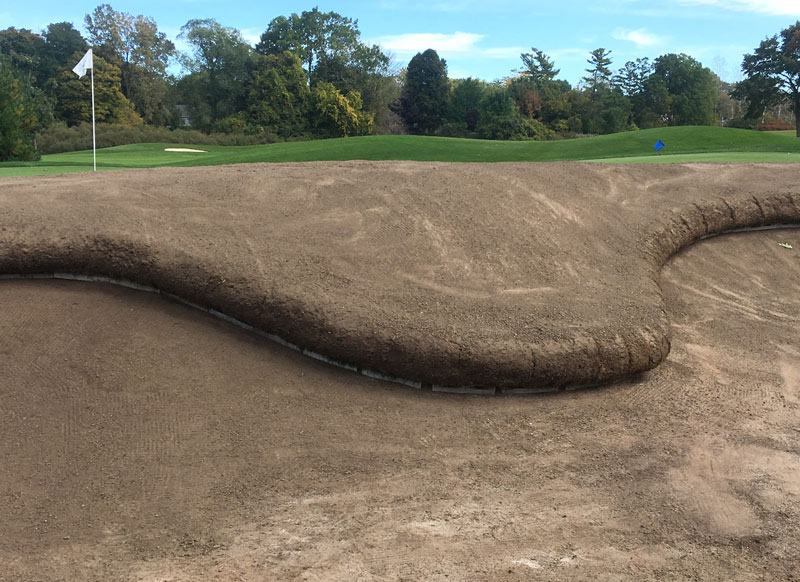
Final shaping of the bunker profile in preparation for sodding.
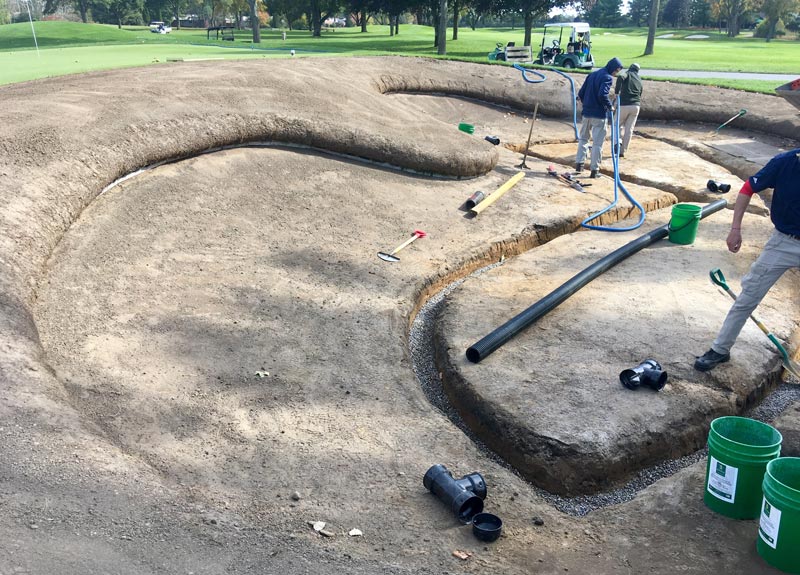
Bunker floor drainage excavation, with an extended toe drain at the base of the bunker wall.

Capillary Concrete installation complete, and Kentucky bluegrass sod wrapped tightly over the bunker’s edge and stapled.
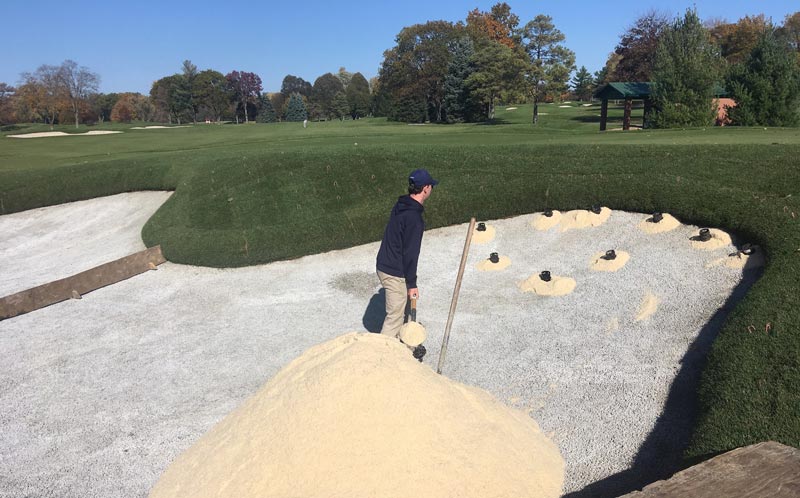
The practice bunker was filled with two different angular sands, compacted and placed at variable depths of 4 to 8 inches. A wooden divider separates the two sand zones in the bunker.
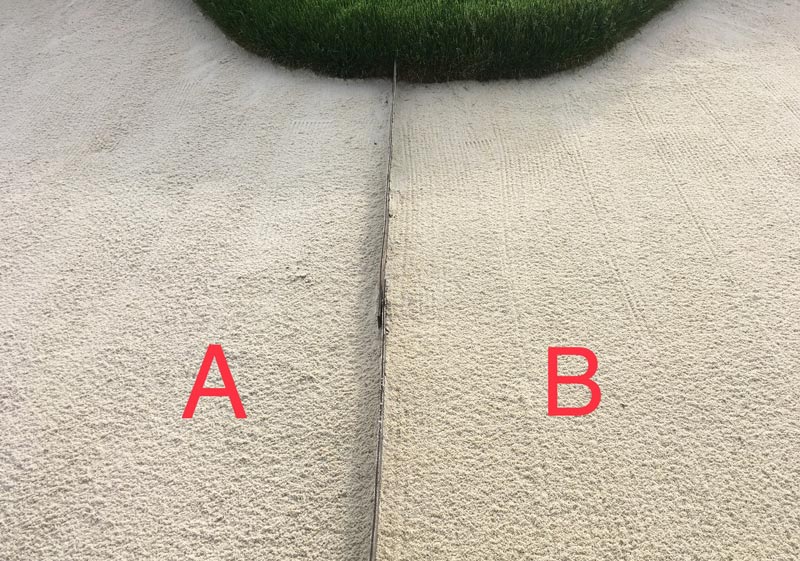
Bunker sand options brought in from Ohio: (A) Tour Grade Signature from Best Sand, Covia Corp.; and (B) Pro/Angle from R.W. Sidley Inc. To prevent bias before final sand selection, no identification of the different sands has been provided to club members this season.
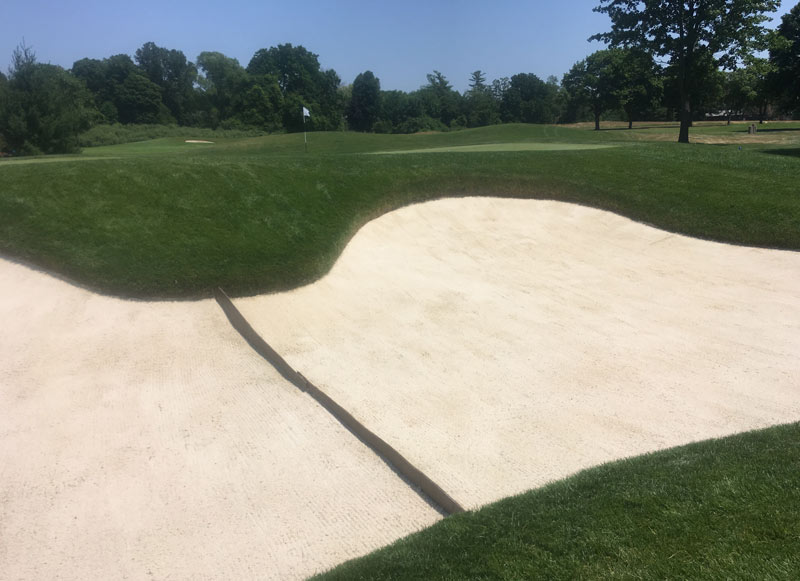
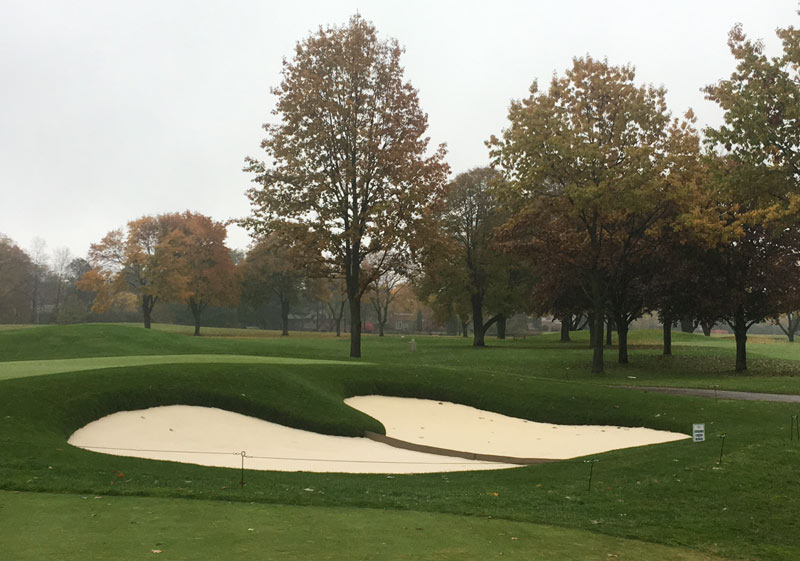
The completed, innovatively edged practice bunker.
London Hunt and Country Club’s members have responded positively to the refurbished feature.
“They love the bunker,” Griffiths says. “The quality of the edge looks fantastic.”
Griffiths is aware his inverted-sod bunker — a board delineates the half filled with Tour Grade Signature sand from the half filled with Pro/Angle sand — doesn’t fit every course, and he readily acknowledges its construction required additional resources. The introduction of concrete blocks and revetted bunkering was necessitated by low clay content in London’s soil. A bunker edge with greater clay content, Griffiths says, could be “shaped just like Play-Doh.”
A prime concern: How does the staff mow it? Griffiths admits he only trusts a few select members of his team to touch up the edges with string trimmers.
He’s keeping a close eye on how well the Kentucky bluegrass handles heat stress from the weather London is currently experiencing, and is using wetting agents and growth regulators to maintain turf health and appearance.
In other words: “A lot goes into it,” Griffiths says. “But no matter what construction you use, bunkers require a lot of maintenance.”
Editor’s note: Take a peek at eight unique, inspired bunkers, crafted to resemble a beloved beagle, a crabby course mascot and more.
Griffiths estimates 25% of his morning labor resources go toward bunker maintenance, and he’s not sure whether his inverted-sod technique will get legs. Work has begun on the second practice bunker — the first has the Capillary Concrete system; the second will feature Better Billy Bunker with turf-type tall fescue sod faces to cope better with heat, drought, insects and sand splash — though Griffiths isn’t certain yet whether he’ll try the inverted-sod technique there too.
Regardless, he’s thrilled with the aesthetics of his first attempt.
“Our bunkers will have to be addressed at some point. Practice bunkers are a great opportunity to test techniques and materials. It all came out of being spontaneous,” Griffiths says. “We came in under budget, and it was a great learning opportunity. We’re still learning.”
Andrew Hartsock is GCM’s managing editor.