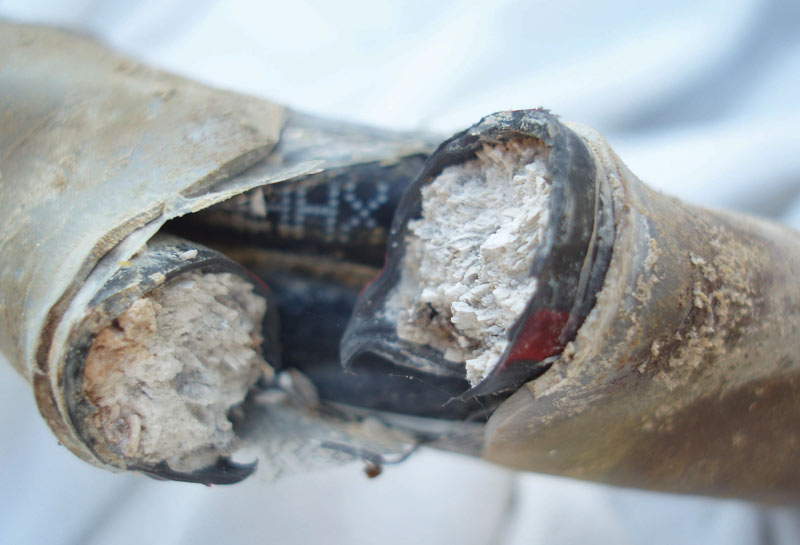
Soil moisture seeped into this aluminum power cable. Metallic elements in the soil reacted with the aluminum and eventually cut through the cable, shutting down power to a garage. Photos by Scott R. Nesbitt
Dramatic, damaging corrosion was the culprit when electric power to our shop failed. The incoming power cable had been accidentally covered by some dirt. Soil moisture containing who-knows-what minerals apparently penetrated the outside insulating jacket. The photo above shows how the aluminum cable corroded and broke apart. A new cable with underground insulation restored power and illustrated how corrosion keeps working until something breaks.
Almost any metal will very slowly exchange electrons and ions when in contact with a different metal. Add an electrolyte — liquid acid, alkali or salt — and the process moves rapidly. Corrosion of metals generates electricity. Alkaline batteries work by mutual destructive corrosion of zinc and manganese bathed in potassium hydroxide. The corrosion is partially reversed in rechargeable batteries, such as Ni-Cd (nickel-cadmium) used for cordless tools.
On turf equipment, destructive corrosion is most obvious near the lead-acid battery used to start and run the machine, because the battery gives off a fine mist of acid fumes. Replace an aluminum water pump mounted with steel bolts, and odds are at least one bolt will show corrosion from coolant liquid seeping into the steel-aluminum joint.
Copper wire grounding terminals connected to a steel chassis will often develop corrosion, shutting down the electrical system. A layer of moist gunk on equipment can provide the electrolyte needed to spawn mutual corrosion between dissimilar metal components that are some distance apart.
Washing off dirt and chemical residues after the workday can ward off corrosion. Use compressed air and/or sunshine to dry off the equipment. Spraying clean, dry equipment with silicon adds a water-resistant layer. But consider that sunshine can corrode non-metallic parts made of rubber, plastic and fiberglass. Ultraviolet (UV) energy in sunlight encourages “dry rot” in rubber tires by helping atmospheric oxygen combine with petrochemicals in the rubber. Plastics become brittle when UV light breaks apart their molecules. UV blocker sprays are readily available at auto parts stores and are worth applying, especially in high-sunshine, hot-weather areas. Petroleum-based sprays are not recommended, because they can degrade rubber and plastic.
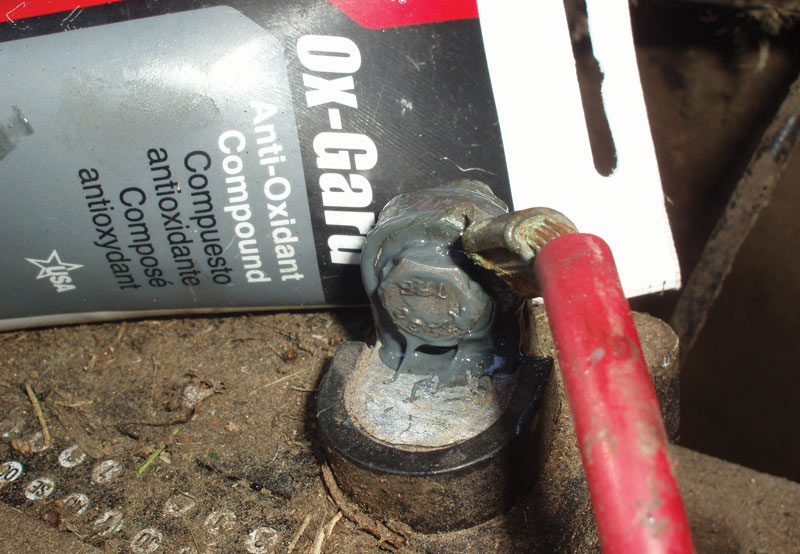
Antioxidant gel that electricians use to prevent corrosion of aluminum wires and components works as a reasonable general-purpose protective coating for battery terminals and as an all-purpose anti-seize and anti-corrosive when working away from the shop.
Specialized anti-corrosives should be used when possible. Antifreeze, for example, contains anti-corrosives that prevent cooling system damage fostered by plain water. Anti-seize coatings help keep nuts and bolts from being damaged by corrosion.
My traveling toolbox includes a tube of electrician’s antioxidant. It’s a zinc-containing conductive gel that’s required to resist corrosion of aluminum wires. I find it works pretty well on battery terminals and as a general-purpose thread lubricant for nuts and bolts. The tube doesn’t spill and it fits in with the tools, and while the product may not perfectly stop all metallic corrosion, it certainly doesn’t hurt.
Scott R. Nesbitt is a freelance writer and former GCSAA staff member. He lives in Cleveland, Ga.