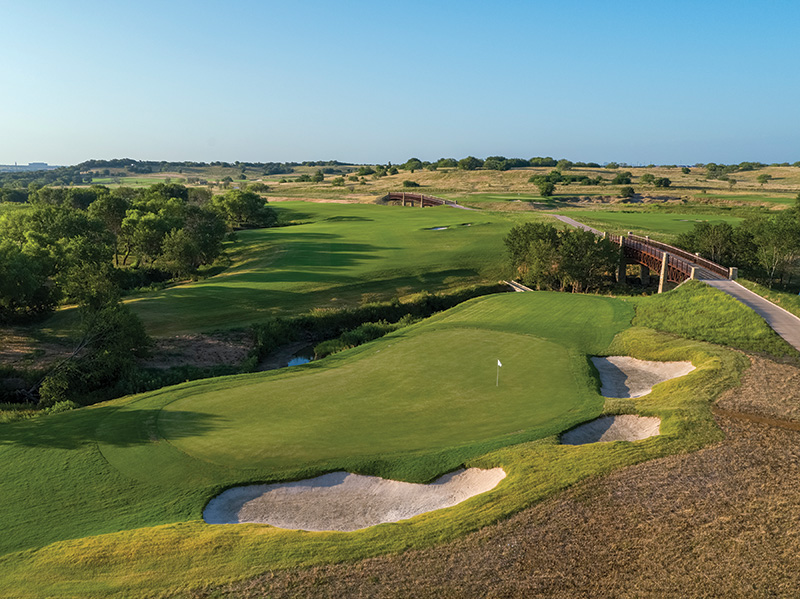
The 18th hole on the Fields Ranch East course at PGA Frisco. On three holes — the ninth, 11th and 13th — geotextile bags filled with sand were utilized to create mounds and retaining walls, a low-tech solution to a challenging construction problem. Photo courtsey of Omni Hotels and Resorts
Stacks of geotextile bags filled with sand would never strike anyone as a particularly sophisticated construction solution. Nor is this “technology,” such as it is, proprietary. But it is new to golf and plenty ingenious, and it may just revolutionize
the way course features are built, planted and maintained.
Yes, planted.
Houston-based Heritage Links built some 2,000 linear feet of geotextile-sandbag retaining walls in Frisco, Texas, on the Gil Hanse-and-Jim Wagner-designed Fields Ranch East course at PGA Frisco, which opened May 2. Steve Stricker won the Senior PGA Championship
contested on the layout back in May.
Once it emerged during construction as the preferred retaining wall solution in Frisco, the geotextile-sandbag drill proved remarkably straightforward, according to Heritage Links project manager Blake Smith. First, start stacking the sandbags. A gripper
— a piece of plastic featuring thin spikes that pierce the layer of the sandbags below it — is placed between each layer. This gripper system interlocks the wall layers. Then, every other sandbag layer is additionally sheathed in a geotextile
fabric that wraps around the bags and extends behind the structure to serve as a sort of anchor.
“That stabilizes the wall,” Smith explains, “but there is an engineering calculation: How much ground behind the wall has to be disturbed because of this geotextile grid? How far back do you need to go? On the 18th at Fields Ranch East,
the grid extends beyond the entire green, so there was a lot of material taking the load off the face of that wall. Where there isn’t so much backing, that’s a vital calculation. You have to get it right.
“But the cool thing is, these individual bags and the finished walls are permeable. There’s enough space in the fabric to allow roots and moisture to go through them, so you can vegetate the wall with almost anything you want. You can also
adjust steepness and create a really natural-looking façade. At 18, we applied hydroseed to the wall, and, over time, it took root and covered everything up.”
“Imagine a gabion basket retaining wall,” adds Doug Wright, Heritage Links vice president of strategic planning, referring to the rock-filled wire cages that traditionally have been used to create and firm up creek banks. “These are
used in a similar manner, in the sense that both are comprised of layering levels on top of one another, until the desired height is achieved. But gabion baskets aren’t flexible; they’re rigid. And they’re not particularly pleasing
aesthetically. These geotextile bags allow for way more subtlety and flexibility. The wall can move in and out, slope back or stand vertical.
“And you can plant it.”
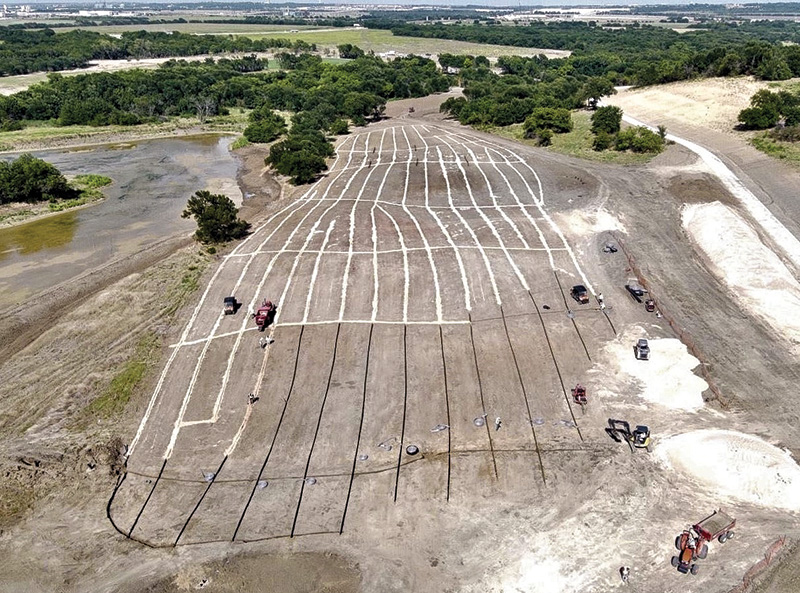
Crews lay in seepage drainage lines on a fairway during the construction of the Fields Ranch East Course at PGA Frisco. Photos courtesy of Heritage Links
Sand solution
Heritage Links eventually deployed geotextile sandbags to construct (and plant) retaining walls on holes 9, 11 and 13 at Fields Ranch East. Most of the structures averaged 10-15 feet in height. At 13, the man-made structure is nearly 20 feet high. Yet
this course-construction technique was first hit upon and vetted at the 18th hole, where Hanse Golf Design and its design team had envisioned something special for the closing par 5 — a wide-but-shallow putting surface guarded by a massive wetland
and a 15-foot retention wall. In the design phase, this façade wasn’t quite vertical. But it was close.
When Hanse and Wagner explained to Smith exactly what the architects had in mind, the Heritage Links project manager didn’t mince words. “We didn’t know how we were going to build that wall,” Smith says. “And we work with
Walter P. Moore Engineering. Those folks can produce the design and engineering necessary to make anything work — and make it look beautiful. They are world-class. But this seemed a very big ask.”
Part of the challenge was the broader, thoroughly rusticated design theme of the course, located 30 miles north of Dallas. For decades, this property had been a working ranch — the old Fields Ranch, as you may have guessed. Hanse and Wagner, for
example, wanted all the bunkers to look as though they’d been in the ground for decades. Other bunkers were deliberately constructed to look abandoned.
Hardscaping these retaining walls didn’t fit with the design ethos the architects had in mind.
“We’ve worked with Gil and Jim and their team on a half dozen projects; we’re building an original, private design for them right now, outside Nashville,” Smith says. “With Gil and Jim, sometimes it can get real challenging
because you don’t have defined drawings. I suppose you could produce the equivalent — in this case, with hardscapes and architectural drawings. But with these two, it’s more often the wave of the hand, or a well-described idea. The
process remains fluid and evergreen until they say, ‘Grass it, boys.’ It’s very challenging, but at the same time so rewarding.
“Originally, we considered artificial rock for 18. There was also the dry-stacked boulder option — most likely north Texas limestone. But that was part of the problem. How do we make this feature look like the old Fields Ranch? Well, it just
wouldn’t, not if we came in and hardscaped it. This geotextile bag structure was the solution because the wall could be planted. That look is what sold our partners at Omni Hotels and Resorts, Gil and Jim, and the PGA, because it was something
you just don’t see on other golf courses.
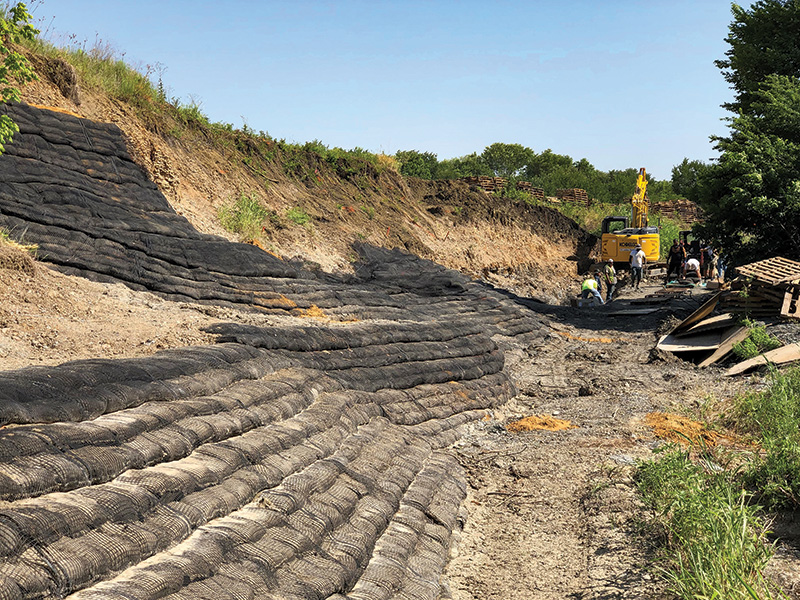
Geotextile bags are installed along the 13th hole of Fields Ranch East Course, one of three holes where this innovative yet low-tech option was utilized.
A tournament test
There’s a lot at PGA Frisco that you just don’t see elsewhere. The sprawling facility features a colossal practice area, a golfing lounge from Topgolf, a 75,000-square-foot putting course called The Dance Floor, a 10-hole short course, and
a 500-room Omni-branded resort featuring myriad food and beverage options and expansive meeting spaces. This public-access facility also is the new headquarters of the PGA of America.
The city of Frisco owns both courses here, Fields Ranch East and Fields Ranch West, a more resort-style design from Beau Welling. The PGA of America holds a long-term contract as on-site course operator and tournament host. An adjacent 2,500 acres are
slated for further development under a master plan from Hunt Realty.
Clearly, the PGA of America envisions a vast, multipurpose, all-in-one golf destination. Yet the driver here has always been championship competition. May’s Senior PGA Championship came first; the KPMG Women’s PGA comes next, in the spring
of 2025. The first men’s grand slam event, the PGA Championship, arrives in 2027. That sequence of tournaments will repeat starting in 2029. While The PGA of America has yet to announce a Ryder Cup for North Texas — based on the existing
schedule, the first available slot for one would be in 2041 — that eventuality feels inevitable.
Accordingly, tournament competition at the highest levels drove much of what HGD envisioned for the championship 18 at Fields Ranch East.
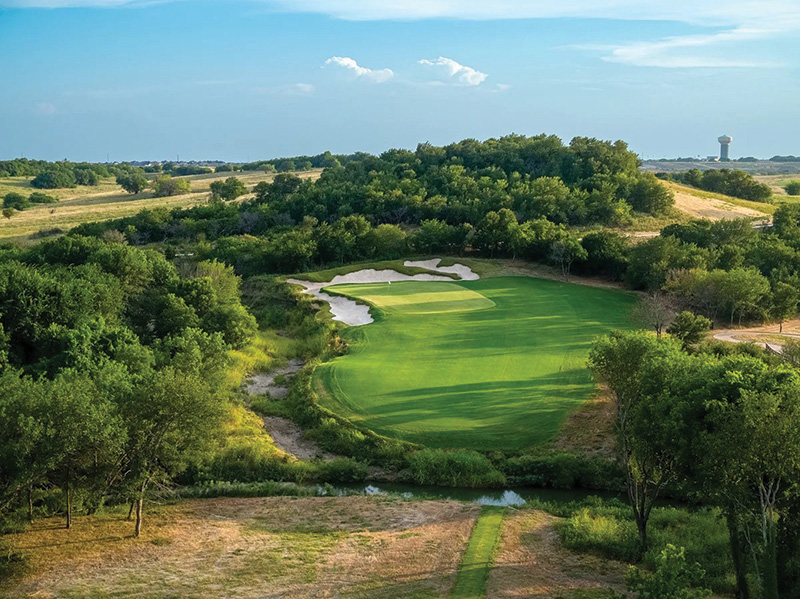
A finished look at the 13th hole.
Water worries
From a course construction perspective, however, water proved the primary driver. An enormous amount of moisture moves through this site from north to south, Wright explains, sometimes at great velocity. What’s more, the inherited soils here were,
in a word, lousy. They were difficult to manipulate when it came to shaping, but they also proved shape-shifting, meaning the clay subgrade could expand up to six inches, then contract up to six inches, depending on moisture content. Naturally,
they also provided for extremely poor drainage.
These are not the type of soil characteristics suitable for achieving firm-and-fast, major-tournament playing conditions.
“That’s why it was so important to construct a golf course where we could control the water flow and moisture conditions in the playing surfaces,” Wright says. “For example, we built an incredibly extensive drainage system at Fields
Ranch East. We installed a product called Turf Drain, which is basically a perforated rectangular pipe wrapped in fabric and placed in a trench — two feet deep by six inches wide — and backfilled with sand. We installed that every 12-15
feet underneath the sand cap. There is approximately 60 miles of this stuff out there. Essentially, it ensures that the golf course will drain within minutes, regardless of any amount of rain.”
Forget the soils for a moment. The Dallas/Fort Worth metroplex is well known for its prodigious spring rainstorms — exactly the season Fields Ranch East will host the PGA Championship and KPMG Women’s PGA.
“We had to build everything to withstand fluctuation in the water levels — and the velocity of flow through the channels,” Wright adds. “Basically, we had to construct many of the course features up and out of the floodplain, and
we used the sandbag retaining walls for this, too. We had to create structures below the actual golf course shaping in order to support the finished grade. Of course, if you build a rock wall or some sort of rigid structure, and you have expansive
soils, how do you keep that structure from being damaged if the soils move?
“You need something with flexibility. While they provide the necessary structural support, the sandbag walls also allow for minor movements in the soil.”
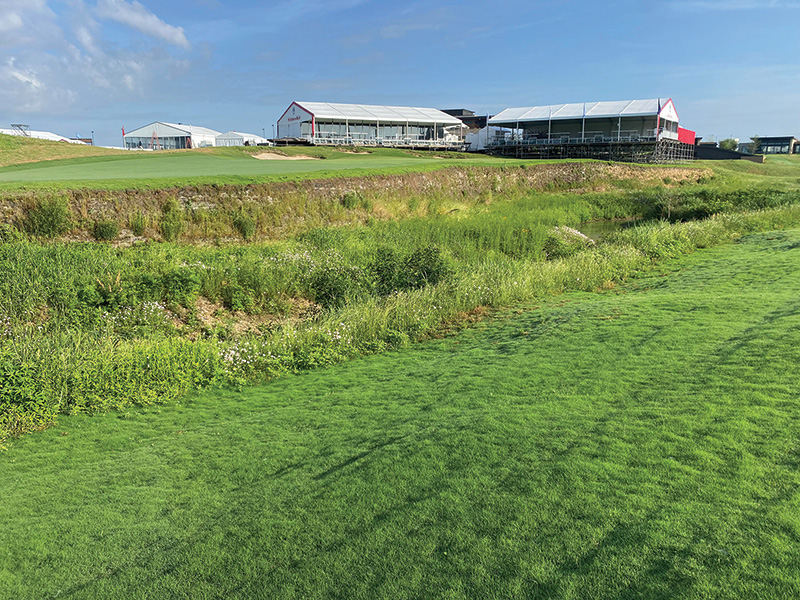
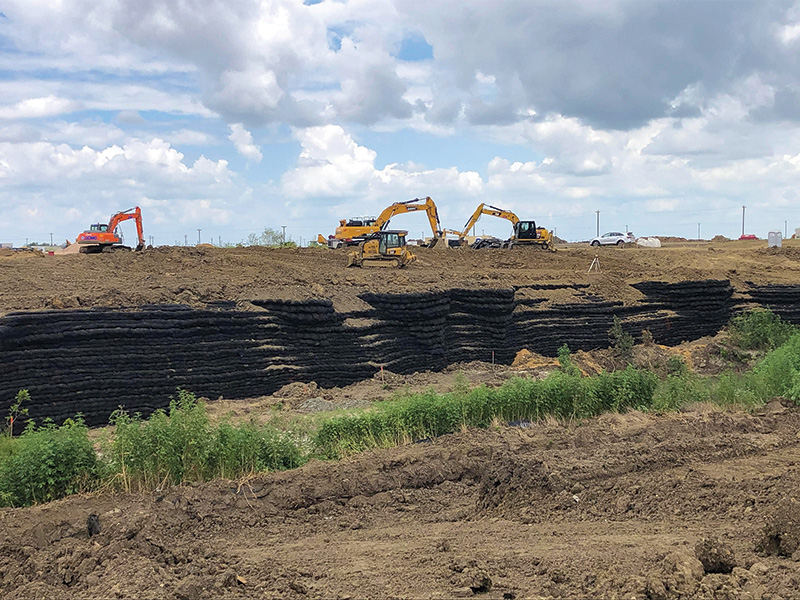
Before and after shots from the 18th hole at Fields Ranch East. The photo below shows how the geotextile bags were used during construction of the retaining wall, while the top photo shows how the sides of that wall grew in over time.
What’s next?
Wright and Smith see a great deal of potential for what remains a very low-tech solution. For these stacks of geotextile sandbags, they envision applications anywhere water flows vary, especially those at higher velocities. They see applications anywhere
retaining soils are necessary. Drainage channels fit this description, of course, yet so do areas around clubhouses and other structures where hardscaping makes little sense.
“On a golf course, aesthetics are arguably as important as matters of stability,” Wright says. “The bag walls were far superior in this regard because of the flexibility we had when constructing them — at varying slopes and elevations
— and the ability to grass them. They can be applied to slopes of virtually any varying degree and can be planted with grass to blend with the rest of the golf course.”
A host of these issues, directives and solutions all came together on that retaining wall at 18. In reality, the entire green complex there had to be excavated down to native, stable soil. Heritage Links then used the geotextile bags and grid system to
construct the retaining wall in 8-inch lifts and to raise it all back up to finish grade. Only then could Smith and his team tackle construction of the actual putting surface and surrounds.
In the broader sense, these durable bags provide something hardscapes simply cannot — porosity. Water is not held back by the sandbags. It moves through at speeds the created structure can modulate.
“Structurally, as you are coming up and it’s compacting, you’re creating a monolithic block. That became 18 green. The façade was integrated into that structure,” Smith says. “There are different products and methodologies
out there, but nothing I’ve used before compares to this system. I hope that somehow we can use it in the future, along creek banks, along high-flow areas, or even along lakes where you need something structural — anywhere you don’t
want hardscape. This option gives architects way more flexibility. Then you choose your plantings. Try as you might, you just can’t plant hardscape.”
Hal Phillips is the managing director of Mandarin Media, an international digital/content marketing firm. He is the former editor of Golf Course News and a frequent contributor to GCM.