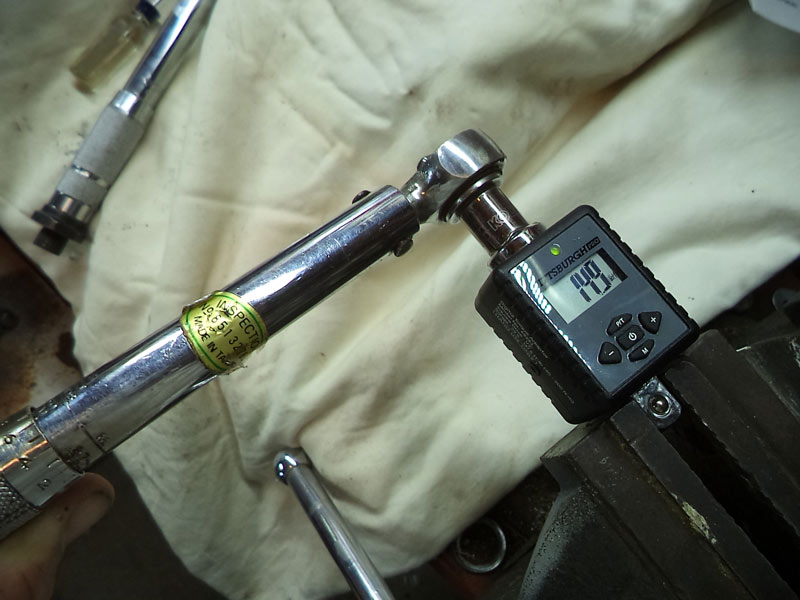
Clamping a digital torque adapter in a vise let us verify that the clicker-type torque wrench was clicking at 14.9 foot-pounds of torque when it was set for 15 foot-pounds. Such adapters can also be used directly to measure torque during machine assembly in the shop. Photo by Scott R. Nesbitt
When bolts are properly tightened, they act like springs and provide the best possible clamping force to hold machine parts together and ensure against failure, and the only way to know whether tight is right is with an accurate torque wrench.
A digital torque adapter makes calibrating torque wrenches easy, and use of such a gauge increases the likelihood that equipment leaving the shop after service will keep performing out on the golf course. There are many brands of torque adapters available at prices that are a bargain if the device helps you avoid a serious mechanical problem or safety issue from a loose or broken fastener.
Engineers have spent the past century designing and testing bolts and other threaded fasteners. Factories draw upon this wisdom to guarantee the bolts in new machines stay tight. Assembly-line torque wrenches are frequently calibrated to provide accurate twisting force that is correct for the fastener. In other words, it’s the bolt — not the parts it’s fastening — that dictates torque. The length of the fastener doesn’t matter — just its diameter, thread pattern and steel grade.
Lots of science goes into developing specific alloys of steel for fasteners. Industry organizations set standards to which reputable bolt makers conform. Bolt heads are marked to identify the grade. Published torque standards assume the bolt is lubricated (engine oil works fine) and that there’s no damage to the threads. Bolts installed dry may require 25 to 30 percent more torque, and dry bolts pose a risk of damaging the mating internal threads, especially if those are aluminum or magnesium.
A 5/16-inch, 18-threads-per-inch (5/16-18) coarse-thread Grade 5 (SAE bolt with three lines on the head) needs 13 foot-pounds of torque. The same size bolt in Grade 8 (six head lines) needs 18.5 foot-pounds. A metric 8-millimeter, 1.25-threads-per-millimeter (8 mm-1.25) bolt looks like those SAE-grade bolts, but the metric with an 8.8 head marking needs 14 foot-pounds while the stronger 10.9 bolt needs 20 foot-pounds.
Those torque figures are minimum values, and service manuals usually specify a range. We just worked on a water pump that called for 8 mm-1.25 bolts that required 14 to 18 foot-pounds. That 4-pound range is the “elastic deformation zone” in which the bolt is actually stretched as the threads pull the shaft deeper into the threaded hole. When removed, the bolt snaps back to its original state and can be reinstalled. An over-torqued common bolt will suffer permanent “plastic” deformation and will lose some of its spring-clamp properties. Modern “torque to yield” bolts for cylinder heads actually take advantage of this permanent deformation. Each head bolt is torqued and then over-torqued by rotating the bolt a specific number of degrees. This makes the bolt longer and somewhat weaker, but the specialized steel alloy takes on better “springiness” properties that let the bolt hold tight during combustion.
To use a digital torque adapter, mount the unit between the wrench and socket. All adapters will beep and/or flash a light when you hit the torque you’ve programmed in via buttons like those on the Pittsburgh digital adapter shown above (sold by Harbor Freight as item No. 68283). Most units beep/flash only when your desired torque is between 30 and 150 foot-pounds — way more torque than necessary for most of the bolts. So, for torque under 30 foot-pounds, you’ll need to be able to see the display, and that’s not always possible in tight spaces.
Most digital adapters are 2 inches long and designed for 1/2-inch drive tools. Most technicians I know use 3/8-inch or 1/4-inch tool sets. To use your usual wrenches and sockets, you’ll have to add a reducer like the one on the wrench in the photo. Chances are you’ll find yourself frequently using your calibrated clicker or beam torque wrench, reserving the adapter for easy-access jobs.
The lack of signal at lower torque values can be resolved with the ACDelco ARM602-3, which buzzes between 3 and 59 foot-pounds and is designed for 3/8-inch drive tools. The ACDelco ARM602-4 has a buzzer range of 4 to 147.6 foot-pounds and 1/2-inch fittings. Both cost about $60 — about twice the price of most competitors. There’s also the BikeMaster RJ7541 adapter, which has a range of 2 to 22.1 foot-pounds, is designed for 1/4-inch tools and sells for about $40.
Manufacturers of digital torque adapters are likely to keep improving their products. Your research on adapter features and prices should include checking out online reviews as well as YouTube video reviews to determine whether such a device would be useful in your shop.
Scott R. Nesbitt is a freelance writer and former GCSAA staff member. He lives in Cleveland, Ga.