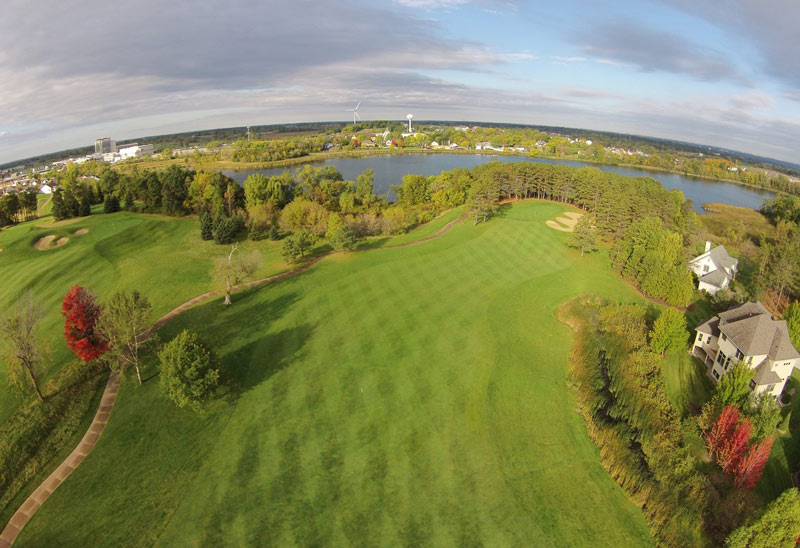
The Wilds Golf Club, an 18-hole public course near Minneapolis, features bentgrass greens (Penncross), tees (PennLinks) and fairways (PennTrio). Photo courtesy of The Wilds Golf Club
Editor’s note: This article was originally published in the November/December 2019 issue of Hole Notes, the official publication of the Minnesota GCSA.
Golfers’ expectations for quality conditions on the golf course are at an all-time high, and in an effort to meet those expectations, the maintenance team here at The Wilds Golf Club in Prior Lake, Minn., spoon-feeds our greens, tees and fairways with soluble fertilizers. By doing this, we can limit the turf’s growth and thatch production, and give the turf just the nutrients it needs.
This is nothing new — many turf managers do this. Our process of mixing soluble fertilizers to apply to greens and tees is quite manageable, as it takes us just two tanks to spray greens and two to spray tees. The challenge arises when trying to mix fertilizer to spray 35 acres of fairways. As a public golf course, we don’t have the luxury of maintenance days, so time management is critical in getting spraying done ahead of play. If we get behind in our spray applications, a four-hour process can quickly become an eight-hour process.
We all have our methods for mixing fertilizers: the bucket and stir stick method, the run-to-the-shop-and-grab-hot-water method, the all too common dump-in-the-tank-screen method. For us, those strategies tended not to work as well as we wanted. The sprayer filters would plug if the bucket wasn’t stirred enough, running to get hot water took too much time, and I’ve had the screen on the sprayer tank fall through into the slurry. Add in aging equipment that lacks the agitation power it used to have, and spray day could turn ugly.
The solution became obvious: We needed a mixing station. The idea first came from a conversation with Superior Turf Services’ Eric Counselman, who’d had a version of a mixing station during his tenure at Somerby Golf Club in Byron, Minn. His station included an induction tank with a pump mounted on a pallet, with wheels attached to the pallet so the setup was easy to put away after use.
We had an induction tank sitting around, and thus my plan was hatched: I would plumb the induction tank, add agitation, and then add a pump to pump the fertilizer into the sprayer. After multiple nights of overthinking this at 3 a.m., I began collecting the parts. Soon, however, my plan took a turn for the better.
It was spring 2019, the weekend of the area garage sale event in The Wilds neighborhood. As I was driving to the golf course, I saw it sitting there, and a lightbulb went off in my head. What has plumbing, agitation and a pump already installed? The Solubilizer 1000! (Actually, at that point, it was just a used but functional washing machine up for grabs at one of the garage sales.)
I approached the homeowner and asked the price. They wanted $50. I wasn’t positive the idea would work and didn’t want to spend any money yet, so I decided to pass. The following Monday morning, the homeowner called me. The machine hadn’t sold. We went and picked it up free.
We plumbed the Solubilizer 1000 directly using the washing machine hookups, and we added an extra water spigot to help with mixing and for rinsing. We then plumbed the discharge from the washing machine pump up and out for easy loading. Our overhead loading system consists of two hoses mounted on three-quarter-inch galvanized pipe for support. There is one hose for clean water for the tank, and one hose for the solution that comes directly from the Solubilizer 1000. We swing the overhead system out when in use, and swing it back and hook it to the building for easy storage.
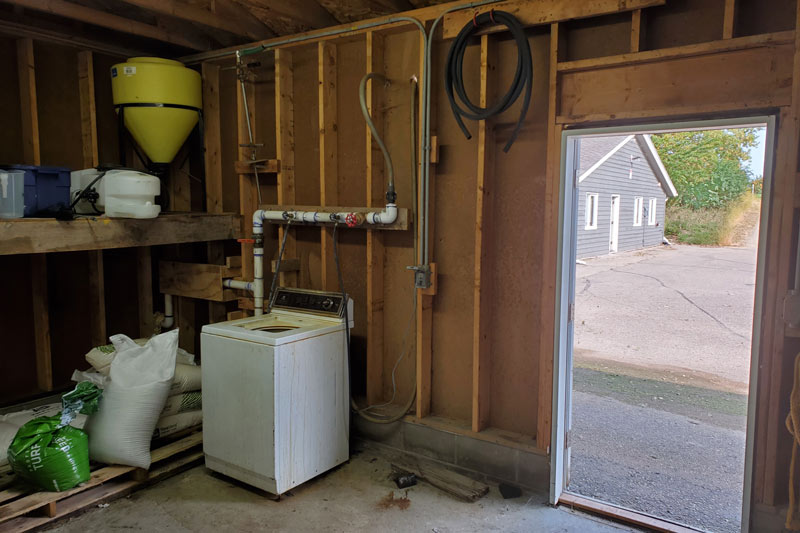
A resourceful superintendent, a humble household appliance, a serendipitous drive to work — such is the story of the Solubilizer 1000. The economical, timesaving innovation resides in The Wilds Golf Club’s chemical shed, which houses all the course’s fertilizers and pesticides.
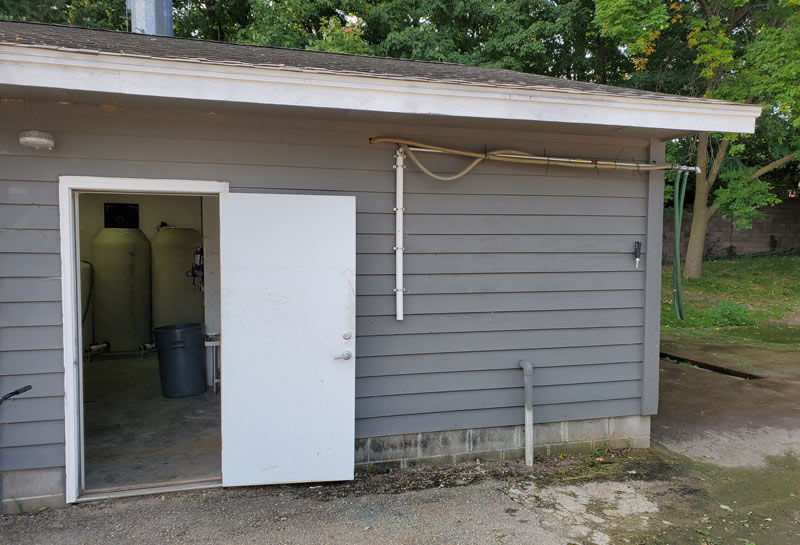
The overhead loading system on the outside of the chemical shed. Photos courtesy of Joe Berggren
The washer is set to the wash cycle to agitate the fertilizer, and it pumps the solution into the tank when set to the spin cycle. (I’m the only one on the crew who has caused it to become plugged up with fertilizer in my impatience to get the next tank out.) The washing machine’s capacity is about 20 gallons of water, and the amount of fertilizer we add depends on how well it “melts down.” Some fertilizers don’t melt down as well as others. We’ve put up to two bags of fertilizer in at a time.
Editor’s note: Discover more “turf hacks” — superintendents’ creative, outside-the-box strategies for better, more efficient golf course management.
Some people have had questions regarding the salt content of the fertilizers and whether that will cause the machine’s parts to corrode. It hasn’t happened yet, and if it does, then we’ll move on to the Solubilizer 2000!
The Solubilizer 1000 cost under $400 in plumbing parts and has been a success for our operation. It has gone over well with our spray technicians and become a point of interest for vendors visiting the course. With 2020 being a record year for number of golfers at The Wilds, having this more manageable and efficient means of mixing fertilizers has definitely been an asset.
Joe Berggren is the GCSAA Class A superintendent at The Wilds Golf Club in Prior Lake, Minn., where he has worked for three years. A 10-year member of GCSAA, Berggren earned an associate degree from Penn State University and a turf certificate from Rutgers University. He won the Minnesota GCSA’s 2019 Watson Award for this article about the Solubilizer 1000.